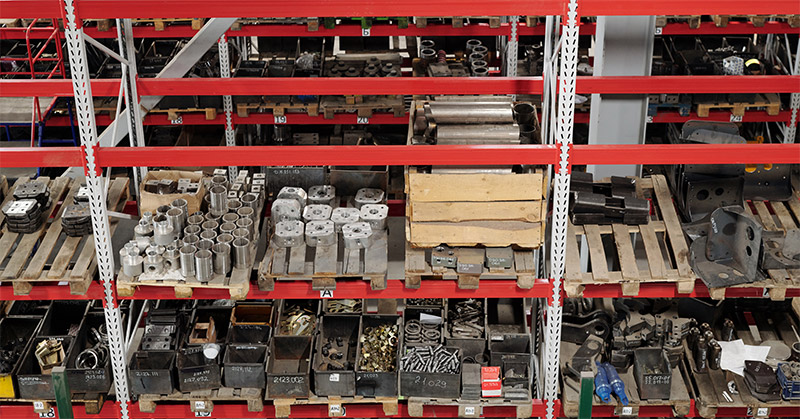
The True Cost Benefits of Using Aftermarket Forklift Parts: A Complete Analysis
For warehouse managers and business owners operating material handling equipment, the decision between OEM (Original Equipment Manufacturer) and aftermarket forklift parts can significantly impact their bottom line. This comprehensive guide explores the potential savings and considerations when choosing aftermarket parts for your forklift fleet.
Contents [show]
Understanding the Cost Differential
The most immediate and apparent benefit of choosing aftermarket parts lies in their cost advantage. Typically, these components cost 30-50% less than their OEM counterparts, representing substantial savings for businesses managing multiple forklifts. To put this into perspective, a standard hydraulic pump that might cost $800 from an OEM manufacturer could be available for $400-500 from a reputable aftermarket supplier.
The cost savings vary significantly depending on the specific component category. Engine components often offer the highest savings potential, ranging from 40-60% less than OEM prices. Hydraulic systems typically show savings of 30-45%, while electronic parts generally cost 25-35% less than their OEM equivalents. Wheels and tires present opportunities for 20-40% savings, and routine maintenance items like filters can often be purchased for 50-70% less than OEM prices.
Quality Considerations and Long-term Value
Today’s aftermarket parts market represents a significant evolution from decades past, with modern manufacturers achieving remarkable advances in quality and reliability. A little-known fact is that many aftermarket parts actually originate from the same factories that produce OEM components – these facilities often run the same production lines with identical materials and quality standards for both OEM and aftermarket products. This factor, combined with sophisticated reverse engineering capabilities and advanced manufacturing technologies, enables many aftermarket manufacturers to produce parts that meet or even exceed OEM specifications. Quality control in these facilities has reached unprecedented levels, with manufacturers implementing rigorous testing protocols and maintaining prestigious ISO certifications that demonstrate their commitment to consistent, high-quality production. To further demonstrate their confidence in product quality, many aftermarket suppliers now offer warranty, that rival those of OEM parts, giving fleet managers and maintenance teams the same level of security they would expect from original equipment components.
Real-World Cost Implications
When calculating potential savings, businesses must consider several key factors beyond the simple price difference. Annual maintenance costs per forklift, fleet size, equipment age and condition, frequency of part replacement, and labor costs for installation all play crucial roles in determining the actual cost benefit. For perspective, a medium-sized operation with 10 forklifts could realize savings of $15,000-25,000 annually by strategically using aftermarket parts for routine maintenance and repairs.
Strategic Approach to Aftermarket Parts
Success with aftermarket parts requires a thoughtful approach to supplier selection and part choice. When selecting suppliers, businesses should verify certifications and warranties, examine customer reviews and testimonials, request sample parts for quality assessment, and compare prices across multiple vendors. Building relationships with trusted suppliers of aftermarket forklift parts can lead to additional benefits such as priority service and volume discounts.
Additional Financial Benefits
The advantages of aftermarket parts extend beyond direct price savings. These parts often offer increased availability, which can reduce costly equipment downtime. The competitive nature of the aftermarket industry drives market efficiency and innovation, leading to better pricing and improved products. Having multiple supplier options provides better negotiating power, and aftermarket suppliers frequently offer shorter lead times for delivery. Many also provide opportunities for bulk purchase discounts, further enhancing the cost benefits.
Practical Example and Long-term Impact
Consider a typical scenario for a 5-year-old forklift. Annual maintenance using exclusively OEM parts might cost around $6,500, including $4,500 for parts and $2,000 for labor. By strategically incorporating aftermarket parts, the same maintenance could cost approximately $4,700, with parts costs reduced to $2,700 while labor remains constant at $2,000. This represents an annual savings of $1,800 per forklift, or $9,000 over five years for a single unit.
Making Informed Decisions
To ensure optimal outcomes when using aftermarket parts, businesses should maintain detailed maintenance records, document cost savings and part performance, implement quality control procedures, and train maintenance staff on proper installation. Developing relationships with multiple suppliers provides backup options and helps maintain competitive pricing.
Conclusion
The strategic use of aftermarket forklift parts can lead to significant cost savings without compromising equipment reliability. When approached thoughtfully, businesses can reduce maintenance costs by 30-50% while maintaining safe and efficient operations. The key to success lies in developing a balanced approach that considers both immediate cost savings and long-term equipment reliability, potentially using a mix of OEM and aftermarket parts based on critical safety requirements and performance needs. Remember that maximizing savings isn’t just about choosing cheaper parts—it’s about making informed decisions that balance cost, quality, and reliability for your specific operational needs.